How to Prevent Downtime with a Proactive Heavy Equipment Service Schedule
Downtime drains profits. Prevent it with a proactive service schedule based on engine hours, usage, and environment. Regular inspections, mobile PM, and telematics help reduce costly breakdowns and keep your fleet productive.
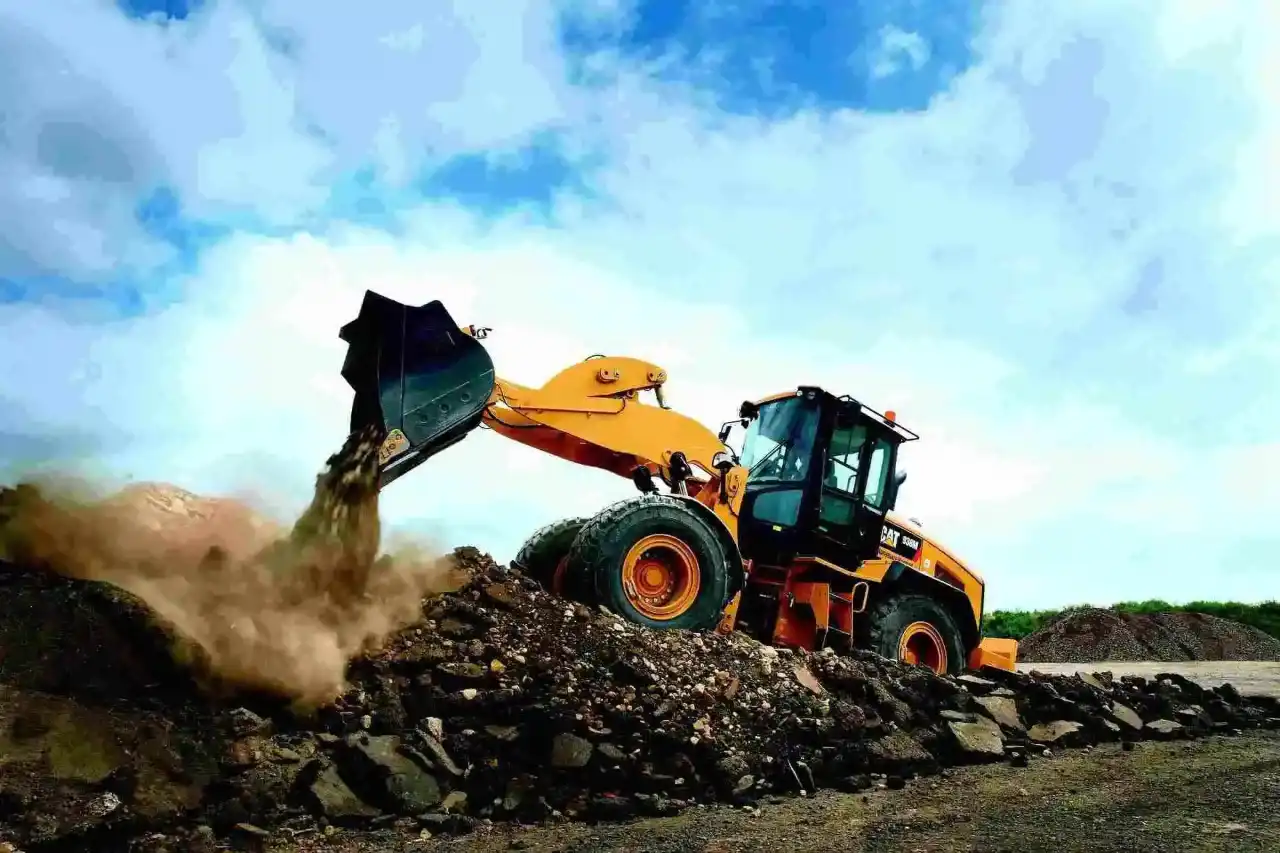
Why Downtime Is the Silent Profit Killer
If there’s one thing heavy equipment owners and fleet managers hate more than expensive repairs, it’s unplanned downtime. When your equipment sits idle, so does your revenue. And while some breakdowns are unavoidable, most are the result of skipped inspections and delayed servicing.
Think about it. Every hour a dozer, excavator, or skid steer is offline, your team is stalled. Your contracts? Falling behind. And your wallet? Leaking cash. That's why a proactive heavy equipment service schedule isn't a luxury—it's the very foundation of operational efficiency.
Understanding the Value of Preventive Maintenance
Preventive maintenance (PM) isn’t just about swapping fluids or cleaning filters. It’s a calculated approach to maximizing uptime and extending the life of your most expensive assets. When done right, it allows you to:
- Detect wear before failure
- Reduce part replacement costs
- Avoid compliance violations
- Maintain consistent job site performance
PM also boosts resale value. Machines with documented service history retain more of their value on the secondary market—a huge win for ROI.
Building the Perfect Service Schedule
The key to effective PM is scheduling. And here’s the secret: base it on engine hours, not just calendar days or miles.
Let’s break it down:
- Light use machines (<5 hours/day): Service every 250 engine hours.
- Moderate use (6–8 hours/day): Tighten that window to 200 hours.
- Heavy-duty, high-vibration equipment: Go even tighter—150-hour cycles may be necessary.
This means knowing how often each asset is used, how it’s used, and in what environment. A compact track loader working in mud will need more attention than one on a gravel lot.
Must-Hit Maintenance Milestones
To stay ahead of equipment failures, here are critical service intervals you must plan for:
- Daily: Fluid level checks, tire pressure, walkaround inspections
- Weekly: Grease fittings, inspect hoses, top off DEF
- Every 250 hours: Oil and filter change, hydraulic filter inspection, fuel system flush
- Every 500 hours: Coolant flush, inspect/replace belts, battery load test
- Annually: Undercarriage inspection, ECM diagnostics, emission system review
If your fleet uses tier 4 final engines, don’t skip exhaust aftertreatment maintenance—DPF cleaning and DEF system inspections are vital.
Tailor the Schedule to Environment and Usage
One size doesn’t fit all in heavy-duty maintenance. Your environment plays a huge role in how frequently equipment needs attention.
- Dusty sites: Air filters clog faster—check weekly
- Cold climates: Fluids thicken—check viscosity ratings
- Urban projects: High idle time means more frequent oil changes
If your operators work across conditions, stagger the heavy equipment service schedule based on operating hours and sensor data rather than fixed dates.
Key Components That Need Regular Inspection
Preventive maintenance isn't just about oil changes. Some of the most overlooked components can cause massive downtime if ignored:
- Hydraulic systems: Look for leaks, cracking hoses, slow cylinder speeds
- Electrical systems: Inspect connectors, relays, and batteries
- Cooling systems: Radiator cleanliness, coolant levels, fan clutch functionality
- Undercarriages: Track tension, wear pads, and roller condition
- Air filters: Reduced air flow can choke your power output and increase fuel burn
Keep in mind, even high-tech equipment with smart diagnostics still needs old-school hands-on checks.
How to Use Telematics and Software to Automate Scheduling
In 2025, there’s no excuse for running your fleet on sticky notes and gut instincts. Modern machines are equipped with telematics systems that feed you:
- Engine hours
- Idle time
- DPF regeneration frequency
- Fault codes
With software like Fleetio, Samsara, or EquipmentShare, you can:
- Set auto-reminders for PM intervals
- Track service history by unit
- Assign tasks to techs
- Generate compliance reports for DOT and OSHA
This eliminates guesswork and helps you stay on top of fleet-wide maintenance cycles.
The Role of Mobile Service in Reducing Downtime
Sometimes the best way to prevent downtime is to never leave the jobsite. Mobile equipment repair and field PM services bring the technician to your door (or site).
For Custead clients operating remote projects, mobile PM means:
- Less hauling to and from the shop
- Fewer scheduling delays
- On-site emergency fixes
- Real-time documentation
Add this to your PM plan, and you’ll turn what used to be dead time into productive uptime.
Training Operators to Be the First Line of Defense
Even the best schedule fails if operators don’t pull their weight. Your crew should be trained to:
- Perform pre- and post-operation inspections
- Report early signs of trouble (leaks, odd noises, loss of power)
- Log hours accurately
Provide quick-reference checklists for daily and weekly duties. Better yet, integrate it into your service software with mobile-friendly interfaces.
Maintenance Documentation: Why It’s Worth Its Weight in Gold
Fleet maintenance is about compliance as much as it is about performance. DOT audits, BIT inspections, and warranty claims all require one thing: proof.
Keep records of:
- Oil samples
- Inspection reports
- Repairs and part replacements
- Fluid logs
When something goes sideways, this documentation helps you prove due diligence, fight warranty denials, or dodge regulatory penalties.
Pro Tips to Maximize Your Service Strategy
Here’s how successful operators keep downtime at bay:
- Use a calendar + engine hour hybrid schedule
- Batch maintenance tasks for similar equipment
- Stock common wear parts like filters and seals
- Rotate equipment use to balance wear across the fleet
- Conduct quarterly reviews of maintenance logs to improve weak points
And most importantly—build a culture of care in your team. Equipment is an investment, not a tool to be run into the ground.
Conclusion
Preventing downtime isn’t about reacting faster—it’s about never having to react at all. A proactive heavy equipment service schedule transforms your fleet from a liability into a well-oiled machine. Build your plan around usage, environment, and data. Make inspections routine. Empower your team. And don’t be afraid to bring the shop to your jobsite.
Because in this business, time really is money—and maintenance is your best insurance policy.
Contact Us
Have questions or want to schedule your truck or trailer in for service? Get in touch with Custead Heavy Truck & Equipment LLC today, we're open Monday through Friday from 7:30am to 4:00pm & Saturdays from 8:00am to 12:00pm.